Individual Subsystems
- PalyRobotics
- Jun 27, 2020
- 1 min read
Updated: Nov 29, 2020
This week each person drew out their design for their individual subsystem, in order to get a better idea of how it worked before they went into Fusion.
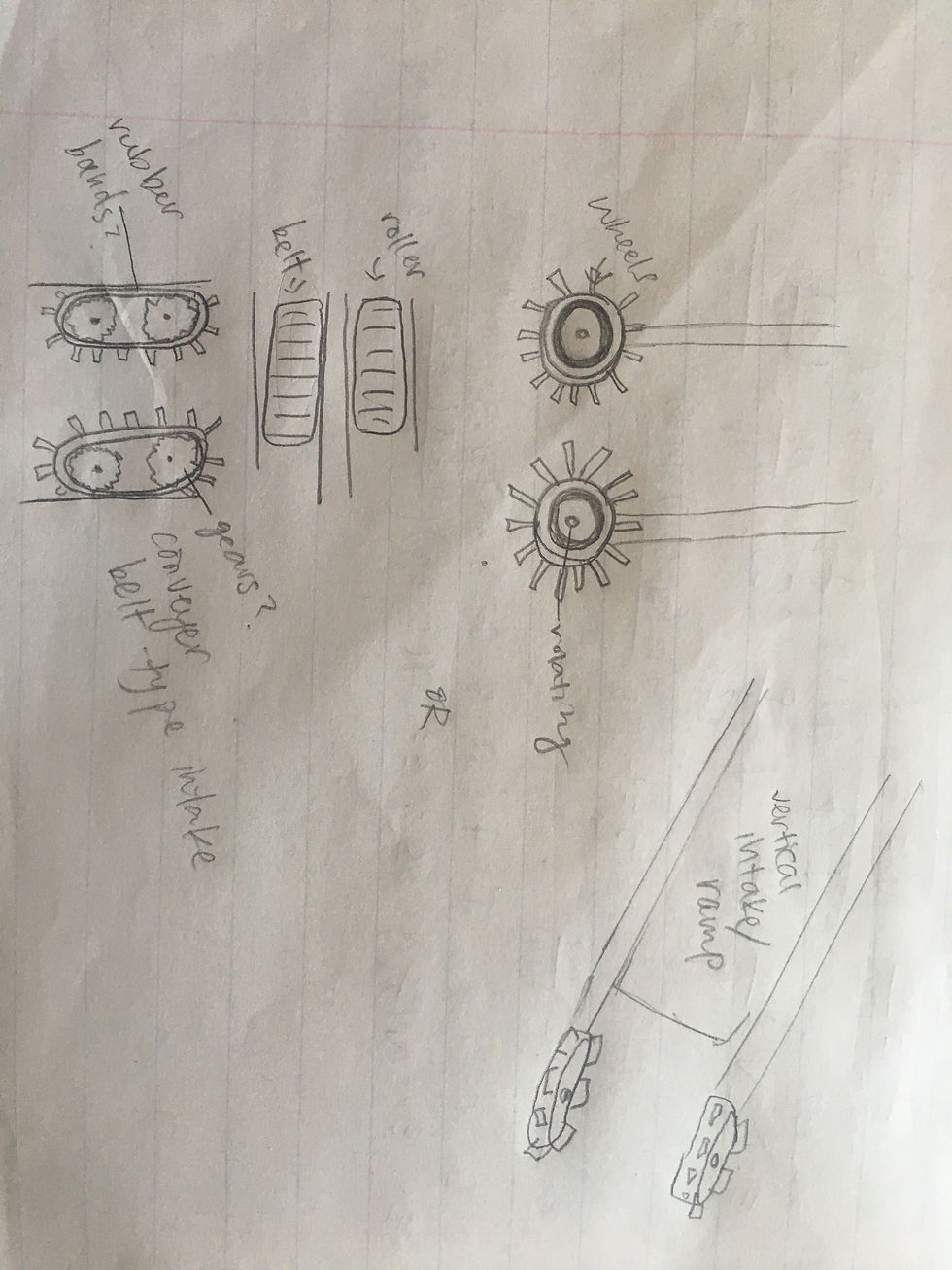
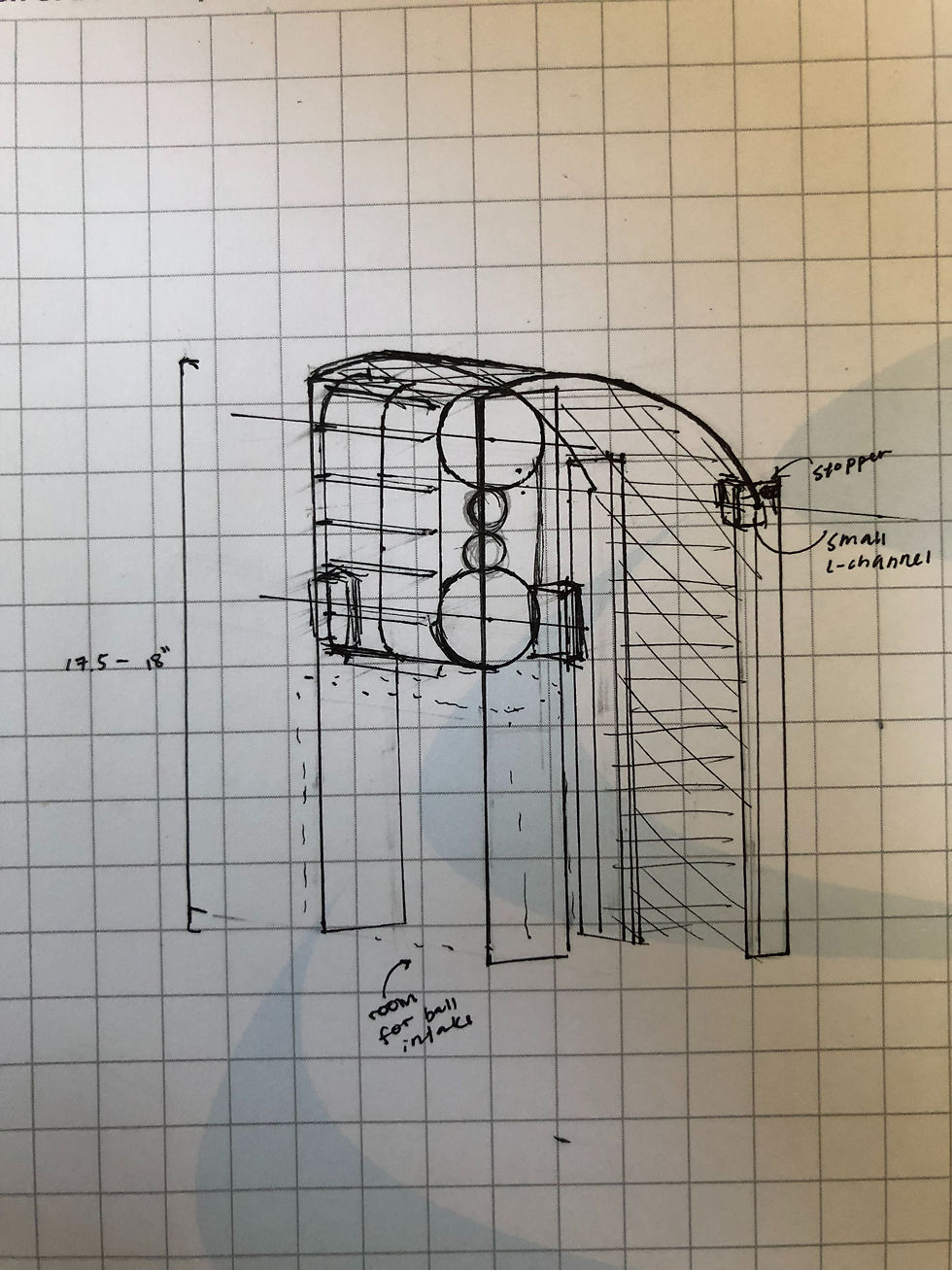
The vertical and horizontal intake looks pretty simple to follow. The vertical intake consists of 1/2 of a tread intake with a metal backing plate and is run by two motors. The side intake is run by tread and will hopefully be elastic to allow the intake to conform to the size of the ball. The hardest part about this will be the transition from the side intake to the vertical one to ensure that there are no stopping points, and to try to make sure the horizontal intake is accurate at picking up balls ( however this would probably be best tested on a physical robot). Additionally, it was brought up that they should probably have a shorter chassis in order for the horizontal intake to stick out.

The hardest part of the lift is the scissor lift. They plan to have a rack gear on the bottom connected to a gear and motor. As the rack gear slides it will bring the two sides of the lift closer together, therefore raising it. We have not had experience with putting together a scissor lift before so it will be interesting to see how it turns out.
Next week we will start working in Fusion to make these prototypes in 3D.
Comments